[This article is WIP and has missing images and incomplete text. Just putting it up to motivate myself to finish – and hopefully it’s useful too!]
Machining composite materials is a lot different than machining metals or unreinforced plastics. Because of the combination of a plastic resin matrix and long reinforcement fibers, the job of a cutting tool is more complicated – it has to make chips and chop fibers at the same time – without making a huge mess of the remaining material. Fortunately there are tons of great products and technologies available to make this happen. This is a guide to types of tooling used to machine composites and tooling materials.
This article discusses machining composite material with spinning cutters, but there are other ways to cut composite materials. Water-jet is the most common and effective. More on that in another article someday, but in the mean time – do some research. It may be a good option!
First lets look at two major factors that determine the performance of tooling for machining: the material that makes up the cutting edge, and the geometry of the cutting and material-evacuating features of the tool.
Cutter Material: Carbide vs. Diamond
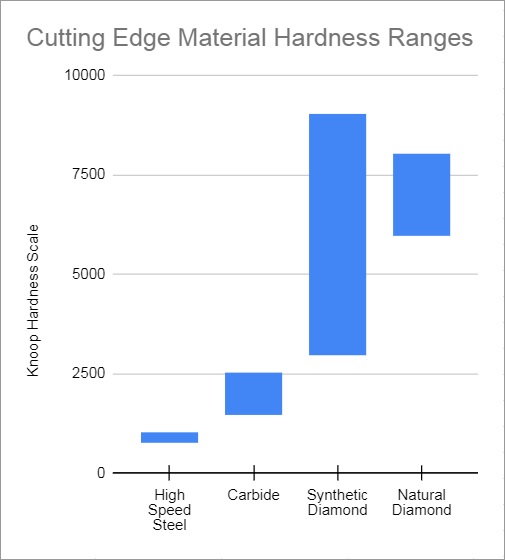
Your two options for the business-end of your cutters will be carbide or diamond. Unless you have a specific application or very limited budget, high-speed-steel (HSS) cutters are a poor choice. Generally, diamond cutting tools will last much longer than carbide, but are many times more expensive!
Carbide cutters are available with a wide variety of coatings and geometries and are the most standard type of tool used in modern machining. Harder than HSS or Cobalt, carbide can give a workable tool life in most materials at a price that doesn’t keep you up at night. It generally gives a good starting point for machining composites – but as you can see from the chart, when it comes to hardness it ain’t no diamond!
There are a bunch of different coatings that can be applied to carbide cutters. These add some measure of performance enhancing quality – hardness, temperature resistance, etc. In some cases these coatings can make a huge difference in tool life and cut quality.
When it comes to diamond cutting edges, there are three overall types: solid diamond edge, diamond coated, and diamond grit.
Solid diamond cutters actually have a chunk of natural or synthetic diamond (mono crystalline) bonded or a chunk of poly-crystalline diamond (PCD) brazed on to the tool to form the cutting edge. PCD is the most common for composite applications – it is less prone to chipping and more tolerant of imperfect machining situations – and generally cheaper! It is made by sintering cobalt or carbide mixed with diamond particles to make a solid chunk that can then be brazed onto a carbide shank. These can often be re-sharpened but it will be more expensive than getting carbide tools resharpened – but cheaper than new.
Diamond coated tools have a thin diamond layer applied over a ground carbide tool to give the cutting surfaces a hard and wear-resistant diamond edge. These are often made with a chemical vapor deposition (CVD) process where 5-30 microns of diamond coating are deposited over the pre-ground carbide tool. Diamond coatings allow for complex spiral and/or interrupted flute geometries with diamond-level hardness and surface durability. For composites trimming and panel cutting, these can be a great choice – especially as they are way cheaper than PCD tooling!
To make things even more confusing there are products that are labeled “diamond-like carbon” (DLC) which often means that they are not exactly like diamond chemically but close! Amorphous diamond is a synthetic crystalline material that can be vapor-deposited (like CVD) and has very similar properties to diamond (natural or synthetic) but isn’t. (You will find that many names mean different things to different people – I have done my best to be right here, but others may disagree! Please let me know where I have gone wrong if you have expertise with this topic.)
Finally, diamond grit tools have a bonded coating of diamond chunks and look like they are covered in very shiny expensive sandpaper. These are more abrasive than chip-making and can have problems with getting loaded up with resin if things overheat. They also hold lower overall tolerances because the cutter itself is made by applying a heavy grit over a machined shank – this grit is less predictable in thickness than a ground edge. They are great for less demanding machining where heat isn’t an issue – or for edge finishing in thick solid laminates.
Cutter Geometry
Because composites cutters have to do the double-duty of machining resin and fibers at the same time, the actual shape of the tool body and cutting edges make a big difference! Resin is soft and tends to clog things up, and fibers are hard and need to be sheared or snapped off cleanly. When you look at cutters designed for composites, you can see a few different overall strategies used to manage this problem.
Tools with many small flutes (cutting edges) do a good job of breaking fibers into small chunks. They also become prone to clogging up with cured resin, especially if friction causes the resin to heat up and get soft. One the other end of things, cutters with few flutes do a good job clearing dust and cut material, but don’t tear fibers into small chunks as readily and are more likely to leave a poor surface finish. Tooling designers often try to solve this problem by making tools with “chip-breaker” and “diamond-cut” geometries.
Some cutters have straight flutes – they are designed to cut without applying any shearing force to the material. The cut puts lots of force on the cutting edges so this is a geometry more likely to last well when using a diamond edge or coating. Chip clearing is not as good as a up-cut spiral cutter and these straight flute cutters do best finishing edges of solid laminate parts.
Spiral-flute cutters are used to introduce a shearing action to the cutting edge and to remove material from the cut by pulling it up or pushing it down. “Up-cut” spirals pull the material up, and “down-cut” spirals push it down. The shearing action can cause tear-out on the top or bottom of a panel but it can also be more effective at shearing fibers.
[Image of cutters]
Compression spiral cutters have a combination of a down-spiral and an up-spiral shape, and are best for machining cored panels. The cutting forces press toward the middle of the panel, pressing skins against the core instead of tearing them off. This geometry doesn’t clear chips well, but it is great for preserving edge finish on panels.
Chip-breaker tools have cutting edges that are interrupted along their length with little notches to limit the length of the chip they produce. For fiber reinforced composites, this works to break (cut) fibers more effectively.
Diamond-cut (has nothing to do with diamond material – the flute geometry produces a diamond pattern) tools have two sets of flutes running counter to each-other – effectively and up-cut and down-cut in one. Both these features make the tools more effective at the dual duty of cutting fibers as well as cutting and evacuating the cured resin.
Your Material Properties Matter
Different mixes of resins and reinforcement fibers cut very differently and require different approaches. Very hard prepreg carbon will cut like an almost-uniform material because the resin content is relatively low and the resin has been cured to a high hardness. You may have fiber tear-out but there won’t be much gumming unless you really bog things down and make heat. With softer resins or ones that haven’t had a full post-cure, you may find that heat is an issue and any rubbing will cause a buildup of resin goo in the flutes of your cutter.
Cutters with more flutes are more prone to loading up with resin and causing excess heat buildup – which leads to melting and smoke and many other bad things. Cut speed and dust clearing also have a lot to do with heat build-up – often coolant or air-blast can help keep things working smoothly. Going slow is also not a solution – it is easy to heat up and ruin a cutter (and a part sometimes) by going too slow. Most cutting tools work best when taking a meaningful sized bite of material. Manufacturers cutting guidance should help here. If you’re cooking cutters, try to speed up your cut and take a bigger cut per tooth – and spend less time making friction!
Types of Cutters
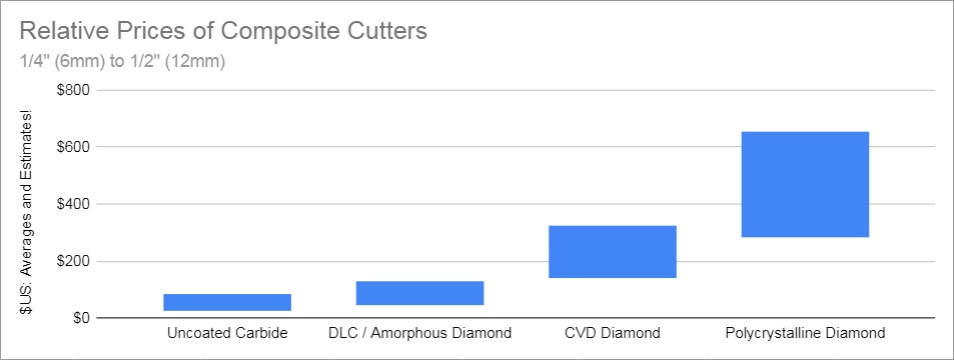
Uncoated Carbide
Solid carbide is a great choice for low-cost, low-stress cutting of most composite materials. For one-off machining or low-volume production, a carbide cutter offers the best value and can give excellent finishes on cut edges. It’ll wear out relatively quickly – and when it does you can replace it. The wide variety of flute geometries available make solid carbide a versatile option – and when you find a geometry you like, often you can upgrade to a DLC or CVD version of the came cutter.
DLC / Amorphous Diamond
“Diamond-Like Coatings” or “diamond-like carbon” (DLC) coatings are chemically similar to synthetic diamond but are applied with a different physical (instead of chemical) vapor deposition process to form a thin very hard coating. These are also called “amorphous diamond” or “amorphous carbon” coatings and are typically thicker than CVD coatings. This can be a benefit in some cases because the cutting edges remain sharper after coating. Generally, they are cheaper than CVD coatings, and my understanding is that they are not the performance-equal to CVD – but are close. Manufacturers use a variety of names for their technologies and aren’t forthcoming about what is actually going on – probably for proprietary reasons – and because it’s confusing!
CVD Diamond Coated
CVD stands for “chemical vapor deposition” which is a process that allows manufacturers to apply a thin coating that is bonded at the atomic level and that is deposited in a very uniform layer. These layers can be as thin as a few microns – a micron is 0.001 mm or 0.00003.9 inches – very small! Typically this deposited layer of diamond “nano-particles” is applied over a carbide tool which has already been ground to shape. While PCD tools require a surface big enough to attach an actual chip of diamond material, CVD diamond tools can have pretty much any flute geometry. This combined with an option to have thicker or thinner coatings (2-30 microns or so) allow for a huge variety in tool parameters.
The real strength of CVD diamond tooling is the mix of hard diamond edges with very specific and complex flute geometry. Many flutes, spiral flutes, chip-breaker and diamond flutes – all of these can be coated with diamond. These tools are probably the most useful diamond cutters for composites (along with DLC – which is functionally very similar) because they offer geometry that is suited to cutting fibers and resin as well as flute geometry that can be optimized for the material. And they’re about half the price of a PCD tool!
PCD
PCD (polycrystalline diamond) tooling has a sintered diamond cutting edge brazed to a carbide shank. This can only work well with tools larger than maybe 0.25″/6mm because there needs to be room for the brazed surface. While multiple inserts can be used on one tool, there isn’t really a way to create complex flutes, so most PCD tools have straight or slightly-raked flutes. The brazing itself can be a weak spot and the inserts can fail in a catastrophic way if subjected to too much heat or a “bump.” When they break or chip they’re pretty much done – but often manufacturers will re-set or repair damaged tools and re-hone. This isn’t cheap but it is cheaper than a new tool.
Diamond Grit
Diamond grit tools are great for blades and edge finishing of solid panels. Mounted wheels with a diamond grit rim can be used in both CNC and manual applications and are an excellent addition to any tool-kit. For production-volume machining, the two downsides of the cutters are wear and loading up of the grit. The diamond particles don’t hold up well to heat buildup or rough use and can chip off leaving… nothing. They also load up with resin if you let things get hot and sticky. Foam cores also tend to melt and load up grit cutters. Better to choose… anything else for cutting foam-cored panels.
Heat
Heat is to be avoided when machining composites! Friction from loaded-up cutters, too-slow feedrates and inconsistent tool-paths can cause resin to soften. Soft resin makes bit-loading even worse and transmits excess heat to the part you are machining. This can cause delamination, weakening, and bad surface finish. Worst-case it can cause fire!
Tool Life
Diamond tooling manufacturers will throw around big multiples of tool life for their products compared to a carbide baseline: 10x, 30x, and more. In some cases this may be true – diamond is an amazing material and if all else is perfect it will outperform carbide by a huge margin. Generally, the thicker the diamond the longer the life – and the more it costs. The drawbacks will be that life ain’t perfect. Things like crashes, tool run-out, fixture loading mistakes, variability in parts and a huge list of other things can wipe out any gain you’d get and leave you crying over a $500 tool. If your process is sorted out enough that you have good fixturing and a reliable machine, ideally in a recurring production situation, you can make out like a bandit by using diamond cutters. Upgrading to the best tooling you can get can be like “free money from the sky” if tool life is really a limiting factor.
Choices
The choice between diamond and carbide depends a ton on your situation and the other parameters present in your production situation.
For a large factory with expensive machines and a well-sorted program, diamond tooling will save time between tool change-overs, improve reliability and probably give a better result. Tool life will really pay off if you get 100 parts trimmed with a $300 PCD diamond tool but can only get 5 parts trimmed with a $30 carbide tool. It costs $3 to trim with the diamond and $6 to use the carbide – never mind the cost of swapping out a tool 20 times more often!
For a small shop doing ones and twos work, you may never see the value of that $300 diamond tool. You’ll definitely be terrified of breaking it with unproven programs and sketchy fixturing. Here is makes sense to use a good quality carbide tool – or maybe a diamond coated tool that costs $100 instead.
Drills
This isn’t about drills but drills are useful! For composites, one of the best options is the “dagger” style drill. These look like pointy two-fluted reamer. They work great, but they don’t clear waste well in deep holes. See also drill-reamer “dreamer” hole making drills. Often it is best to machine holes in a CNC situation, especially if the holes are larger.
For hand drilling, brad points are the go-to. And hole-saws are also super useful. Carbide grit hole-saws are an excellent choice and are less likely to tear laminate than a toothed hole-saw. Best to come at a thick or cored part from both sides using a pilot hole to eliminate tear-out.
Be careful to avoid over-heating the area around the hole. Starting and stopping deep holes and using a vacuum or compressed air to clear chips and dust really helps. Friction is the issue and thermoset resins don’t recover well once the smoke starts!
Contributors
Thank you to the people who answered my questions and shared pictures!
Additional Resources
If you have a link you would like added, please let me know! I would like to provide as complete a list of resources as possible. This is just a first go / place-holder and not an endorsement of any of these products or companies.
Manufacturer’s Tooling Guides
- Kennametal: Aerospace Composite Machining Guide
- Harvey Tool: Ideal Tooling for Machining Composites
- GDP Industrial Tooling: Diamond v. Carbide : Weighing the Costs and Benefits
- Crystallume: CVD Diamond Coated Rotating Tools for Composite Machining (PDF)
Carbide Tooling for Composites
Diamond Tooling for Composites
- GDP Industrial Tooling (GUHDO) PCD
- LMT Onsrud: Composites
- Emuge Fiber-Cut
- Lach Diamond
- Amana Diamond Tipped PCD
Diamond Grit Cutters
Bodi Company: Diamond Products
Drills
Pan American Tool (Dagger Drills)