History…
It used to be that when you wanted a big plug or one-off mold, you built a wood pattern and glassed it, sealed it, and rubbed miles of sandpaper over it until it was perfect. Pattern making was (and still is!) a highly skilled job and the results an experienced craftsman can produce are excellent even by today’s standards. Almost all production composite parts until around 1990 were built on plugs that were hand built. In the 1980’s CNC (computer numerical control) equipment started getting large enough and accurate enough to actually machine big surfaces directly from CAD models. This was pretty awesome, but it brought new problems.
The Paste Process
Pioneering CNC plug builders tried lots of things before finally settled on the idea of using a cheap low-density urethane or EPS foam material glued in huge blocks to a wood or metal support frame. higher density foams are expensive, so the goal is a cheap low-density bulk substrate with a thin, stiff, hard shell just on the surface.
First, foam is glued oversize to a stable wood or metal frame. The big CNC is used to machine away foam to a surface that is maybe .5”/12mm below the final surface. Then it gets a layer of fiberglass over the light foam – which provides local stiffness and the potential for vacuum integrity. On top of the cured fiberglass a layer of “tooling paste” provides a high density, easily-machinable surfacing layer. The CNC then machines this tooling paste to a final surface. There is still plenty of sandpaper work to do, but the machine leaves the surface fundamentally fair and the finishers job is to keep the geometry while bringing the whole surface up to a high gloss.
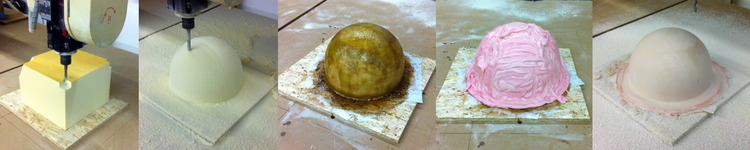
This process is pretty ideal from a composite perspective. Each material does what is supposed to do. The low density foam gives lots of volume for a low price, the glass provides stiffness locally and vacuum integrity, and the tooling paste gives it a nice hard machinable surface. Sometimes for small patterns that won’t need vacuum integrity, the paste can be extruded right on top of the foam.
Check out this example project that shows the construction of a small plug with polyester sprayable paste.
Epoxy vs. Polyester
Tooling paste (also called putty, compound, etc.) is like tooling board in a sprayable or extrudable form. Most products are a thermoset resin with a large volume of filler added to make it easy to machine. The two primary categories to choose from are based on two kinds of common resin chemistry: polyester and epoxy. Each of these has benefits and drawbacks. Generally, epoxy is more stable and provides a tougher and more thermally stable surface. Polyester is cheaper, faster to apply – but less stable and more likely to crack or warp.
Polyester Tooling Paste
Polyester putty is like special Bondo that comes in a huge drum. Typically this is either sprayed or dispensed like toothpaste from a tube. For large volume use, a drum un-loader with metering pumps for the putty and catalyst are the standard method. Hand mixing is really hard, and streaks of un-catalyzed putty are no fun.
Some benefits of polyester paste:
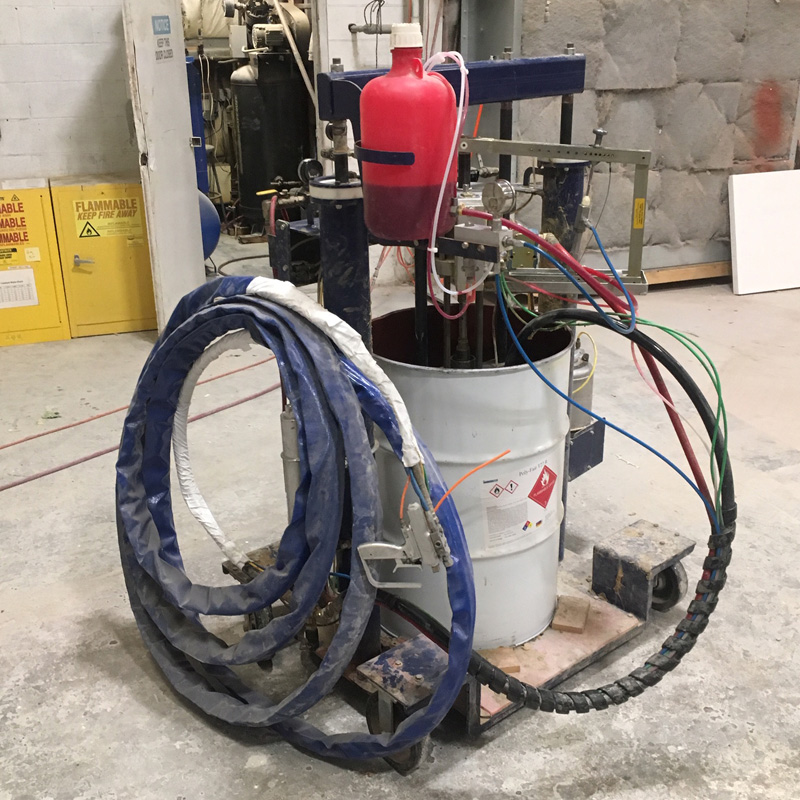
- Price – its cheaper by a lot.
- Extrudable or sprayable options available
- Cures fast
- Goes on over a layer of cheap, easy to laminate mat and resin
- Dispensing equipment is way cheaper ($20,000 or less)
- Fully compatible with polyester/vinyl-ester primer systems
- Smells awesome
- Likely less of a health hazard than epoxy (though this is up for debate)
Some drawbacks of polyester paste:
- Not as stable as epoxy – shrinks unpredictably and sensitive to catalyst ratio
- Cracks easily – often days or weeks after it would have been easy to fix
- Doesn’t get along chemically with cheap EPS foam – products available to (mostly) fix this
- Doesn’t cure completely right away so machined chips are extremely flammable
- Smells terrible
Epoxy Tooling Paste
Epoxy paste is usually supplied as parts A and B of a 1:1 to 3:1 mix ratio. Both resin and hardener parts are filled to a similar viscosity and they are either mixed by hand or dispensed from a 2-component metered-mix machine.
Some benefits of epoxy paste:
- Stable surface, minimal shrink during cure.
- Good thermal resistance
- Good adhesion to EPS foam
- Consistency
- Good adhesion to polyester or epoxy laminates
Some drawbacks of epoxy paste:
- Expensive
- Dispensing equipment is much more expensive ($80,000+)
- Health risks of epoxy exposure
- Most common products are extrude-only, which is labor-intensive
- Slower cure times
The biggest benefit of epoxy paste is the stability of epoxy in general. Typically epoxy is used with EPS foam – the white stuff that looks like little balls glued together. EPS is about half the price of similar weight urethane foam. EPS foam off-cuts and dust can also be recycled. With fiberglass/epoxy laminate between the foam and the paste, it is all similar chemistry, and not fussy about shrinkage or material thickness.
You can make a beautiful surface with either polyester or epoxy, but many of the largest and most demanding plug builders use epoxy for large surfaces.
When Paste?
Generally if you’re building something big, your options are to hand-build a pattern/plug or use a paste-based system. It is my opinion that hand building has become underrated. Big machines are rare and expensive, and a team of skilled carpenters and pattern makers (or even some college students on a Formula SAE team) can build a very nice, cheap, vacuum tight mold surprisingly quickly. But that’s a story for another day… our question now is when do we go from machining a tooling board product to using a paste system?
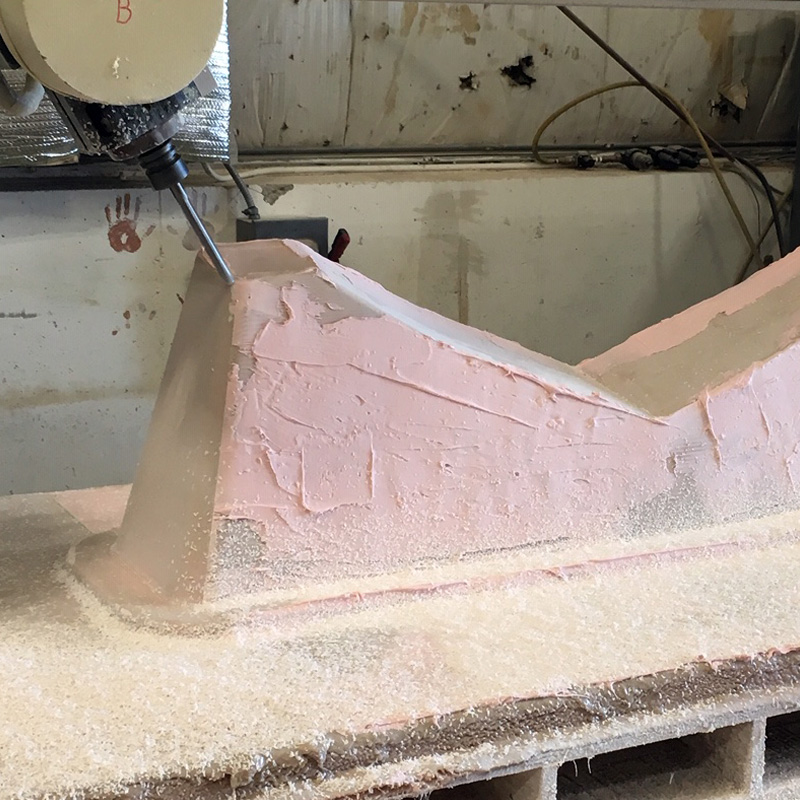
I’d say as a rule of thumb, if its bigger than a car – go paste. Ok, maybe a couch or a refrigerator! Like all rules of thumb, this one has lots of holes in it! If you have a long flat thing that can be easily machined from blocks of tooling board, then that’s a great plan. If you have a bunch of smaller things to shape at once, go ahead and use paste – the many steps will become an asset for scheduling and the material is probably cheaper. Also, paste based tooling is lighter and easier to move around without damage.
So: is your part bigger than a couch? Go paste. Smaller? Go tooling board!
And if you’re trying to build a mold for low temperature prepreg or plan to posture on the paste plug – be careful! Just because the tooling paste has a high Tg/HDT (the temperature at which the resin system starts to soften and become flexible) that doesn’t mean that the substrate (foam, steel, wood, fiberglass) will behave nicely. You also will have a huge piece of insulation on the mold surface of your part. It can be done, but I would strongly suggest you do the math on a plug and then a composite tool. Wacky stuff happens even below 100C! There are lots of good infusion and tooling systems that can get you a high temperature mold off a low-temperature plug.
Extrude vs. Spray?
Some tooling paste products are designed to be sprayed onto the substrate. Others are meant to be extruded – like giant beads of toothpaste laid parallel to each-other over the whole surface.
Spraying typically takes multiple passes and an experienced operator to get a uniform coat. Extruding is a slow and highly skilled manual process – if you are to avoid air between the beads and the endless lines of voids to be filled after machining. Both are pretty much the worst!
What you do depends on the product you choose.
Polyester paste is usually sprayed – though there are extrudable products – and epoxy is usually extruded. Extrudable polyester paste can have serious shrinkage problems unless the catalyst is dialed in just right (and even then…) and I have had it bend metal frames and de-laminate fiberglass from foam substrates as it shrinks. This sucks and is not easy to fix. It is great for small parts though.
Epoxy paste is almost always extruded. Dragging a hose all over a huge surface and carefully laying beads of material with a minimum of air pockets is a hard days work! I am terrible at it! It is one of the major downfalls of tooling paste – it’s a ton of work and a real art to get it right. Some large format CNC machine builders can integrate paste extrusion into the CNC system, so the machine lays paste with robotic precision. I have seen videos but haven’t done it. My guess is that is makes little financial sense to tie up an expensive machine that could be milling with sub-millimeter precision for the purpose of doing what a skilled human could do outside the machine envelope… but it looks cool.
Conclusions
Paste is an excellent option if you are a tooling producer – or are looking to hire one for your project. If you’re looking to job-out a tooling job, you should be able to get excellent advice from the supplier(s) who quote your job. This is a process that benefits from scale and experience! Make sure you specify your requirements very carefully. Temperature, finish level, flange size and details of assembly… there are lots of variables and it’s worth making a big effort to get the mistakes sorted before things get glued together.
It really doesn’t make sense to own the tooling paste equipment unless you have a big 5-axis CNC router and are going to invest in the skills and team to do this on a regular basis. You will be committing to a big increase in skilled paint and finish work. There are lots of steps involved and each benefits from skilled labor. The extruding and spraying steps require practice. For me, with a 5’x10’x3′ 5-axis, the paste was really only economical for very large stuff if it could be done in batches. After a few years I determined it wasn’t worth it – best to subcontract large jobs to a specialized tooling builder and machine smaller tooling from board products. As your equipment gets bigger, it makes more sense!
Appendix A: Tooling Paste Products
- Scott Bader: Crestamold T27 and T28 Tooling Compounds
- Sika Advanced Resins: EP and PUR Modeling Pastes (SC 175, etc.)
- Gurit: T-Paste 70-2
- Rampf: RAKU TOOL Close Contour Pastes
- Freeman Supply: Specialty Tooling Pastes
Appending B: Large Format Tooling Service Providers
Please get in touch if you’d like to be included in this list, and in our ‘Resources’ section.
North America:
- Janicki Industries (WA, USA)
- Design Concepts (FL, USA)
- Symmetrix Composite Tooling (RI / NV, USA
- Bayview Composites (WI, USA)
- VarneyCNC (ME, USA)
South America:
Europe:
- MonsterCAM (UK)
- Persico (Italy)
- Metyx Composites (Turkey)
- Baltic Tooling (Estonia)
- Knierim Tooling (Germany)
Asia:
Australia / NZ: