People have known for thousands of years how to mix materials together to make something that is more than the sum of its parts. By using one material to compliment another so that the best available material is used for the job, different materials “team up” to make more effective and efficient structures. In the last century or so have we learned to combine materials to exceed the properties of structures frequently found in nature. The main way we do this is by applying huge quantities of energy to make very highly-refined materials and then carefully controlling their combinations and chemistry. This refining, engineering and careful combining of reinforcements and polymers is the composites industry.
If you look at the most complex and high performance items built by people – think rockets, airplanes, race-cars, satellites – most of these use composite materials to give them incredible mechanical properties for their weight. You just can’t build things this strong, stiff and light without teaming up polymers with particular properties and highly engineer-able reinforcement fibers.
Specific Strength and Stiffness
It is this performance for a given weight that is so incredible. Specific strength is a measure of strength divided by density – specific stiffness is the modulus of elasticity (E, aka. Young’s Modulus) divided by density. Here is a chart showing the specific strength and specific modulus of a variety of materials:
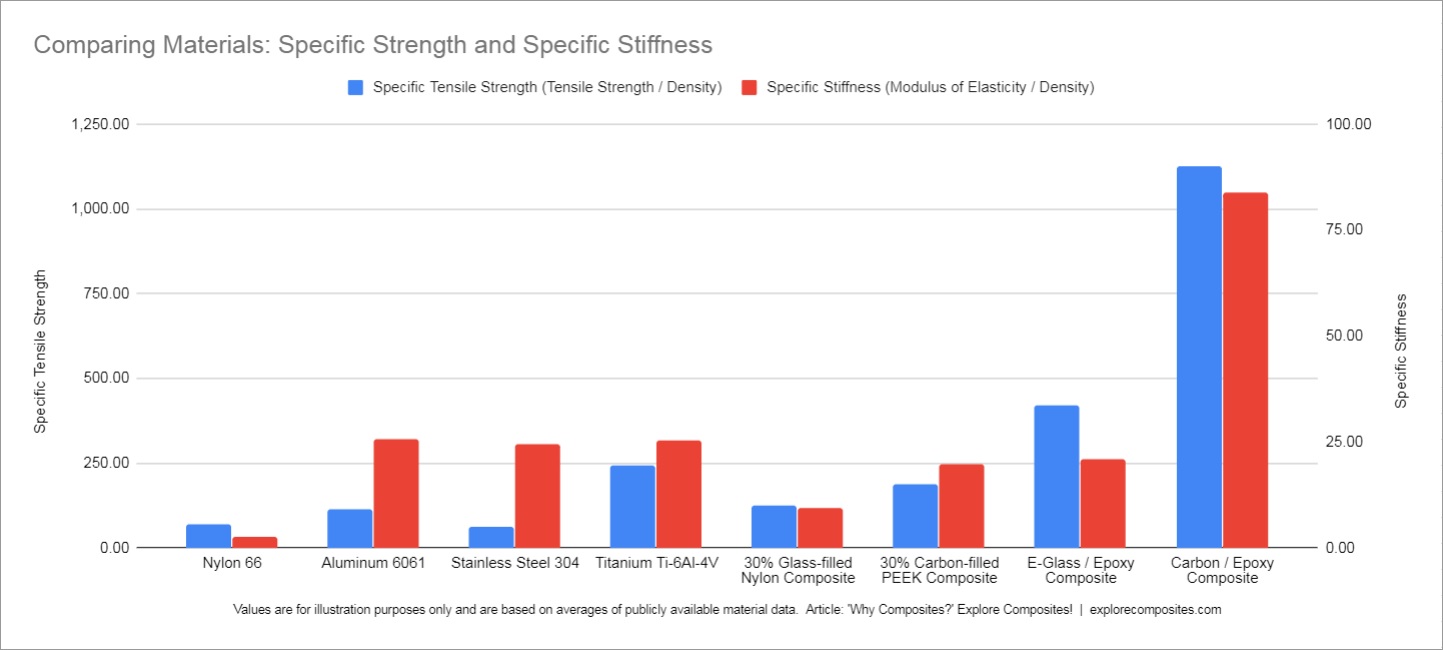
It is pretty clear with just a quick look that composite materials have extraordinary engineering potential! But the benefits don’t end there.
Superpowers
I like to think about three composites “superpowers” – the really compelling reasons to use composite materials. The first superpower is the option to make “anisotropic” layups – with reinforcement material pointed only in the direction of given loads. Superpower two is core. Cored “sandwich panel” composites offer unparalleled stiffness for their weight. Superpower three is the ease of making tooled surfaces with complicated geometry and nice surface finishes – and doing it over and over without out extra work.
Superpower #1: If you look at a piece of wood, it is very strong in one direction and very weak in the opposite. The tree trunk needs fibers running up and down to resist bending in the wind and collapsing under its own weight, but across the “grain” you find it only needs to be strong enough to keep everything together. Plastics and metals aren’t like this. They are what engineers call “isotropic” – the same in all directions (mostly). A piece of titanium is very strong for it’s weight – but the main way to engineer it is to modify the geometry, rather than the properties of the material itself. Composite materials are “anisotropic” which means their properties are direction dependent – and this is what makes them awesome! It also makes designing and building with composites complicated.
Superpower #2: The cored “sandwich panel” is a way to make composite panels super stiff and also super light-weight. By pushing all the load-bearing material to the very edge of a panel and filling the neutral middle area with a light weight material with good compression and shear strength it is possible to let all the materials play to their… strengths!
Superpower #3: Because most composite materials are laminated over/in forms called “molds” – they can be made to take the exact shape and surface over and over for every part. Like injection molding – each part can be shiny and smooth with no real extra effort. Compared to fabricated metal which will always need priming and painting for each new part – large runs of composite parts can get their complicated geometry and shiny finish for very cheap – once the expensive tooling is made.
So the big reasons to use composites are:
- You want to optimize the orientation of the strength and stiffness of your materials – taking advantage of the anisotropic nature of fiber reinforcement. Composites allow for an amazing level of “design density” and structural specificity in a component.
- You need a high stiffness or strength to weight ratio and you can’t get it with other materials. “Sandwich” construction with composite skins on a light weight core can get you results unobtainable with any other material.
- You want a material that is UV, rust, corrosion or fatigue resistant – and strong.
- You have an assembly made up of multiple parts that can be combined into one part if molded from composites.
- Maintenance is a concern and molded composite parts can have a longer service life than metal ones.
- You need good mechanical properties AND a complex shape – and you need to replicate it many times in a manufacturing environment.
- You’re building something awesome and carbon fiber is awesome – so you kind of have to!
Ok, the last option is NOT a good reason. But it is too often THE reason people choose to build with composites. Don’t do this – it’s wasteful and it undermines the idea that materials justify their own use by being a best fit for the process and demands of the application. If you want to skin the dash of your car with carbon to impress your buddies, that’s fine, but if you are designing real products that will be made over and over – please choose a more responsible material!
There are lots of great reasons to use composites, and if it’s the right fit you can do amazing things… but be sure that some other material that is less resource intensive (and maybe recyclable) can’t do the job just as well.