This article is about how to go about CNC machining surfaces with curves and corners and geometry that isn’t just flat sheets. Almost all composites tooling will have some features like this and there are easy ways to plan your machining and ways that work less well. The goal here is to go over basic strategies for planning stock, roughing and finishing – and doing it as fast an accurately as possible!
Once you have a 3D model of a part and a plan for your molding method you can start modeling the features you’ll need to actually build it. Splitting a more complex part into chunks so that multiple molds can be used, figuring out how to assemble the chunks, drawing flanges… pretty soon you have a model of an actual plug or direct-mold surface. This article is about how to use a CNC machine to mill away everything you need to leave a surface that looks as much like the 3D model as possible. Here’s that example part again:

Here we’re looking at a small part (aka “the part”) that we’re going to make using some kind of vacuum bagged operation – wet layup, infusion or pre-preg. We’re going to need some flanges on that mold. I’ve cheated the top flange down, with the idea that if we need more in that direction, we can just put a radius on the top edge and continue the mold over the top. For infused parts this would be really useful. For pre-preg or wet-laid parts where there is less “peripheral process material” we could make the flange way smaller and envelope-bag the whole mold. Choices, choices! For the purposes of this article, we’ll keep the flanges.
Planning and Decisions
So we started with the part on the left (white), and after deciding which side was going to be molded, modeled the (red) female mold – shown here with the part in it. From that mold surface, we modeled the plug (gray) on the right, which will form the surface of that red mold. So we need to mill that plug. We’re imagining that we’re going to use a pretty standard 3-axis CNC router and are going to machine this from some nice quality MDF or urethane tooling board, which we’ll seal and prime and make nice and shiny before laminating the orange mold off it.
At a first look, I’m concerned about getting a cutter into the inside corner on that plug. Super long milling tools are chatter-prone and hard to deal with when you have limited z-stroke on your machine. Having to machine the plug in two pieces and glue them together after is also best to avoid if you can – but if not that’s fine – it’s pretty easy. If you have a 5-axis or a robot arm then never you mind about this step – you can just lean over and reach in there. But for this router, we’re going to tip the plug back to open up that near-vertical wall a bit so we can get a reasonable-length cutter in there without hitting things. Watch out for collet nuts and spindle noses when planning a cut – it’s all too easy to hit the part! Like this:

Stock Layout
So there we have our plug surface modeled up – and I have taken the liberty of adding a sheet on the bottom to give us something to hold onto when clamping this down to the machine – and so there’s a little extra material under that shallow spot in the middle. Now we’re going to draw the block of tooling material that we’ll glue together to machine. We could make a huge “bounding box” block but it would take forever to rough-machine and would waste material. We’re not going to make it super fussy either – just close enough to be easy to assemble AND have minimal wasted volume.

You can see the gray blocks assembles in the four images on the left. They are bigger all around than the finished model, mostly so the glue-up can be a little “off” without being a problem. The bottom layer is made of stacked sheets to the needed height (always a multiple of the sheet thickness) and each remaining block is made out of easy-to-cut rectangles stacked up. Check out the image below. I like to pull these details out and draw each layer and each of the pieces of tooling block material that will be needed. This is faster to do in the computer than with a tape measure and a marker pen. You’ll still need those for measuring and marking – just not for thinking.
For MDF patterns, molds and plugs, I recommend you check out the article on HOW TO USE MDF FOR COMPOSITES TOOLING. It covers some of the same things, but has lots of information about MDF-specific challenges and how to deal with them.

The solid model of the stock will become your stock model for the CAM operation. The stock model tells the CAM software what material it has to machine away in roughing strategies. Keep in mind that you need to be very careful gluing up your stock model, especially if it is detailed. The machine only knows what you tell it and if your real stock doesn’t match your CAD stock you’re gonna have a problem. I sometimes model the CAM stock models 1/2″ (12mm) or so larger than the actual glued up model. This way I cut a little air but don’t take a huge dive into the material if it isn’t glued up just right.
The article on MACHINABLE TOOLING BOARDS has some more information on gluing up blocks and how to align layers.
Roughing
Roughing is the first operation in a machining process, where the bulk of the excess material is removed. Here we see the stock model after two different roughing strategies. On the left, the “3D Adaptive” option in Autodesk Fusion360, and on the right a traditional stepped roughing option. The calculated time for each of these was about the same, but the steps are much smaller on the Adaptive-roughed stock. There are lots of good resources for learning CAM software, so I am not going to go into it in a big way here. This is more about how to get good results on 3D surfaces without wasting a ton of time.

When dealing with large blocks of material – often thicker than the stick-out on your cutters, it is really important to be careful about crashes. With tooling board or MDF, it is going take only seconds of rubbing a collet face or burying a tool holder onto the part before you have a fire on your hands!

The roughing toolpath on the left above is constrained by the red line shown on the upper right. This looks good! The same toolpath run without the constraint creates a big bad crash as the tool tries to go around the perimeter of the surface. When designing your tooling it is important to remember where you can machine and plan for the limits of tool length and toolholder diameter. Sometimes it is good to model in a surface to control where the cutter can go – like adding a step to that back edge or modeling in the perimeter trimming depth. Be careful to keep tool stick-out as short as possible – especially for roughing. As a rule of thumb – longer tool = slower cut and more chatter.
Finishing
Moving on to finishing operations, it is important to keep in mind the load on the cutter, especially if you are using a long skinny one. You want the cutter to experience similar loads as it goes – because if it has to plow through thick areas and then breeze through thin ones it will deflect and leave a poor surface finish. This is one reason why the Adaptive roughing strategy above yields a better result. The smaller steps leave a more even tool load for the finishing tool. If you need a really nice surface or have to finish with small tools, it may make sense to do a “pre-finishing” pass – essentially a second roughing operation that gets within 1/8″/3mm (or much closer depending on material density) of the finished surface. This will leave a constant depth of material for the finishing cutter so it will not flex and chatter as much.
Vertical “Waterline” Finishing

The first part you need to machine is the “vertical” part of the surface – shown on the left above. Here that is everything between 45 degrees and vertical. CAM software will let you define the slope range for an operation. The operation here is called “Contour” or sometimes “Waterline” finishing. The tool goes around the surface at a given height and then steps down a small amount (the “step-down”) and does it again – over and over down to the bottom. This is best done with a ball-end cutter. If you don’t do the vertical first, then the parts of the horizontal path that get close to vertical surfaces may have the cutter plowing into a vertical wall of unmachined material. This is noisy and will cause chatter, gouges and frustration. By doing the vertical parts first, you have clear access to the base of the walls for your horizontal paths.
A quick note on holes! If you have modeled holes in your 3D geometry, be mindful that a roughing operation offset from the surface may not have roughed out the holes if they are near the cutter diameter. It may be necessary to avoid (cover temporarily, exclude, etc.) the holes for finishing operations so you don’t have a cutter trying to stab down into a hole that isn’t pre-drilled. This is one other reason to do contouring cuts first – which will gently (if slowly) machine the holes without a crash/cutter breaking situation. You may also want to do holes with a separate drilling or boring operations before you finish the main surfaces.
Horizontal “Planar” Finishing
The second part to machine is the “horizontal” part of the surface – shown on the right above. Here I told the CAM software to machine everything between 50 degrees and horizontal. I went with 50 degrees so this path would slightly overlap the vertical area and not leave a messy ridge. The operation is typically called “Horizontal” or “Parallel” finishing and the cutter goes back and forth across the flatter areas of the surface machining and stepping across a given “step-over” – which is the equivalent concept to the “step-down” in Contour finishing above.
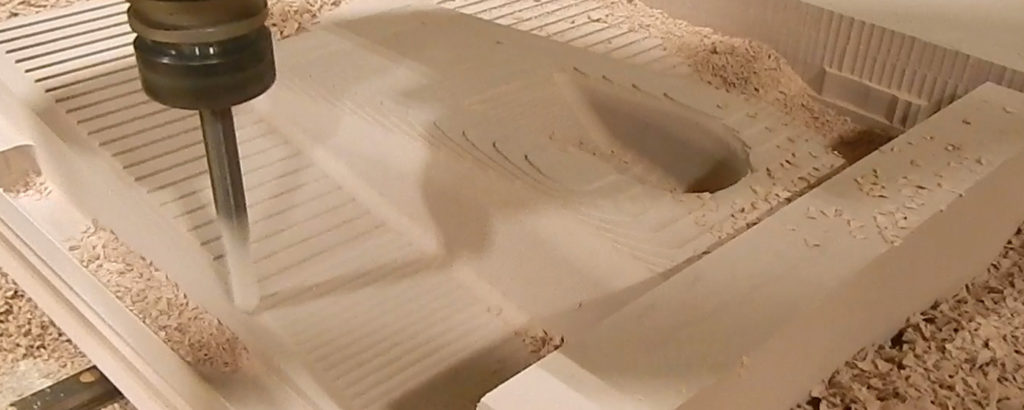
Below, the finished tool-paths all together. On the right you can see the overlap on the radii of the Contour (vertical) paths and the Parallel (horizontal) paths. Because of that 5 degree overlap, we have complete seamless coverage.

Step-over and Cusp Height
The amount you step down or across depends on your desired surface finish, cutter ball diameter and how much time you have. I would typically finish MDF or tooling board up to 40lbs/cubic foot with a 1/4″ (6mm) to 1″ (25mm) ball-end cutter. For a 1/4″ (6mm) cutter you could get a nice ready-to-sand finish with a .02″ (.5mm) step size. For a 1″ (25mm) cutter you could step down .04″ (1mm) or more. You can draw a circle in CAD that is the diameter of your cutter and them move a copy of it over by the proposed step-over. The “cusp-height” is the amount of material left in the little ridge between the passes – it looks like this for a 1/2″ (12mm) ball-end cutter stepping over 0.04″ (1mm) – the cusp height is 0.0008″ – not a huge deal!

Finishing Details
Of course here our radii are all fat and easy and we can finish the whole thing with one tool. In reality, you may need to come back and finish local areas with smaller tools. This can be done by constraining the machined area for each operation. Be careful to zero your tools to the same reference. Even a very small error can lead to steps in your surface that are hard to remove.
Pencil Finishing
If it is just the radii that need work, you can come back with what is called a “Pencil” path and trace the inside corners. Even if you don’t have to change to a smaller cutter, this is a good idea to clean up the spots where the two kinds of paths meet and overlap. A pencil trace path can clean up gouges and chatter. See the left-hand image below.
On the right below, we have one final trace tool-path to clean up the extra material we added to pad the block of stock material. You could do with with a grinder, but if you’re like me you’ll be tempted to machine the perimeter nice and tight just so it looks good. It can also be a valuable trimming reference for your finished parts – especially if you considered this when designing the mold and made the mold edge an offset of the part edge!

Random Tips for Success
Only use cutters just long enough for the job. It can seem like a good idea to use a really long ball-end mill for finishing, and if you need to that it fine. Longer cutters flex and chatter more and if you have inside corners, this can lead to ugly surface finishes. Longer cutters will need to be run more conservatively.
Consider pre-finishing surfaces where you are using small finishing tools or where you want the best surface finish. It is worth re-machining inside corners with the finishing tool, leaving only a small amount of stock before you run your real finishing paths, as larger cutters will have left lots of excess stock in there.
Get to know the smoothing, look-ahead, trajectory planning, or path-tolerance features of your CNC control. Look into how smoothing features in your CAM software impact the code you generate and how the controller handles this. Here it is handy to have a commonly used machine control and CAM package so lots of other people will have had the same problems and written about them on the internet!
Next Steps
An this is just the beginning! It’s a good place to start if you’re new to this but soon you’ll be venturing into other CAM options and testing how much time you save by making your glued-up stock better match the surface model. It is a never-ending game – trying to improve and learn and at the same time come up with standard recipes that just work.
Have a look at how machinists plan and “CAM-out” metal parts with 3D surface machining. There are lots of great resources available on the internet and on YouTube. The sooner you learn to think like a machinist and plan your setups and strategies from the beginning, the easier it will be. Take the time to learn about work offsets and tool length compensation. There’s so much that plays into the speed, accuracy and smoothness of your finished surface.
More specific details of this process will be covered elsewhere on this site in the future, but for now, hopefully this provides a sold foundation.
Additional Resources
Change Log
Updated 1/9/21 – formatting and image